We put our technical expert Peter Goodwin under the spotlight to gain his perspective on developing a high quality testing laboratory, in order to share his expertise.
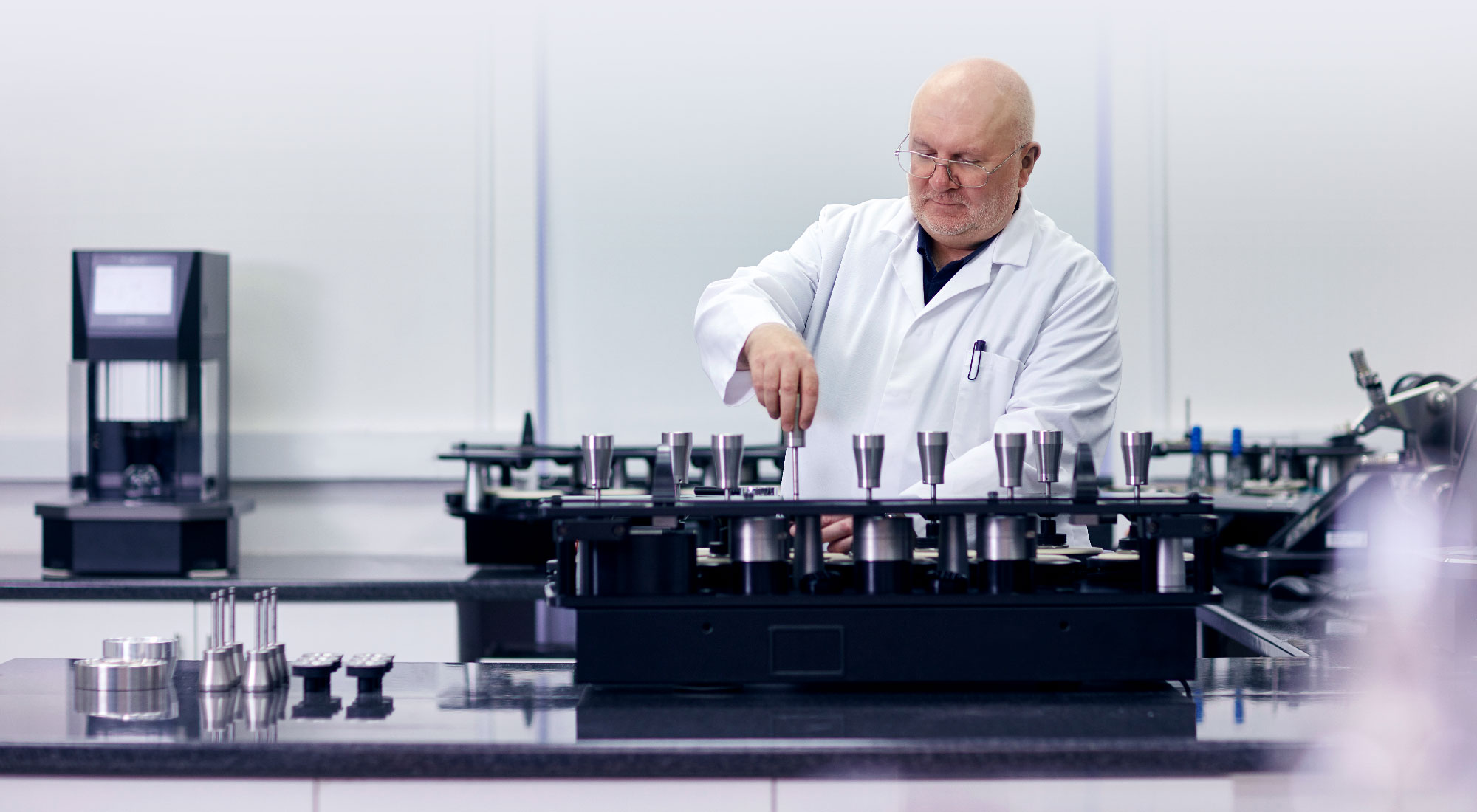
Developing a reliable testing laboratory that provides accurate and correlateable results is a critical part of business strategy for all factories and test houses.
A good testing laboratory allows a factory to have control over every aspect of its operations. If the factory is under control; it has satisfied customers, increasing business, a growing reputation and maximum profit.
Accurate and correlateable results are only possible if a laboratory is planned, built and developed in the correct way. It's not just about buying testing instruments
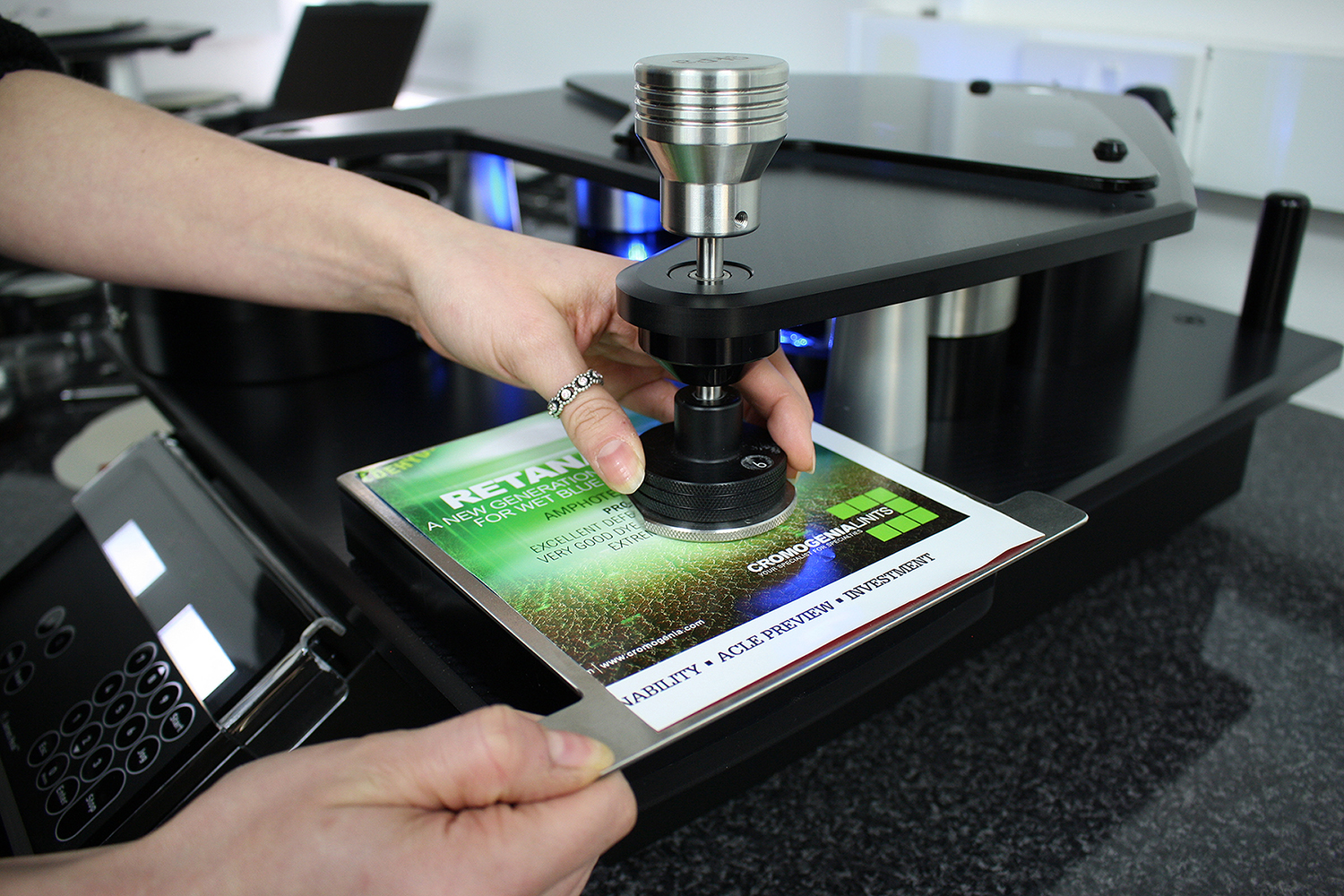
As a starting point, it's all about results, says Peter. 'Accurate and correlateable results are only possible if a laboratory is planned, built and developed in the correct way. It's not just about buying testing instruments,' explains Peter.
'It's about buying accurate and reliable instruments, accessories and consumables and locating them in the correct environments as determined by the test methods. It is also about the need for establishing 'Good Laboratory Practices' amongst conscientious, properly trained and motivated staff.'
He continues, 'The need for early and comprehensive planning plays a vital role in this - mistakes, things that are forgotten and ill-informed decisions made during the planning stage often cost a significant amount of money to sort out later. If this has to be done at a time when the factory has developed to a point where it relies on the laboratory to provide test results to support production processes - it may be very disruptive.'
It's about buying accurate and reliable instruments, accessories and consumables and locating them in the correct environments as determined by the test methods. It is also about the need for establishing 'Good Laboratory Practices' amongst conscientious, properly trained and motivated staff
So what do you need consider when creating a new testing laboratory?
Firstly, consider size requirements. The size of a testing laboratory and the number of rooms required depends on many factors, such as:
- Immediate and future volume of testing
- The test routines that have to be carried out
- The current and projected future buyers
- The budget that is available; and, most importantly
- The commitment of the Chief Executive to the principle of Quality Management and reducing risk
The need for early and comprehensive planning plays a vital role in this - mistakes, things that are forgotten and ill-informed decisions made during the planning stage often cost a significant amount of money to sort out later
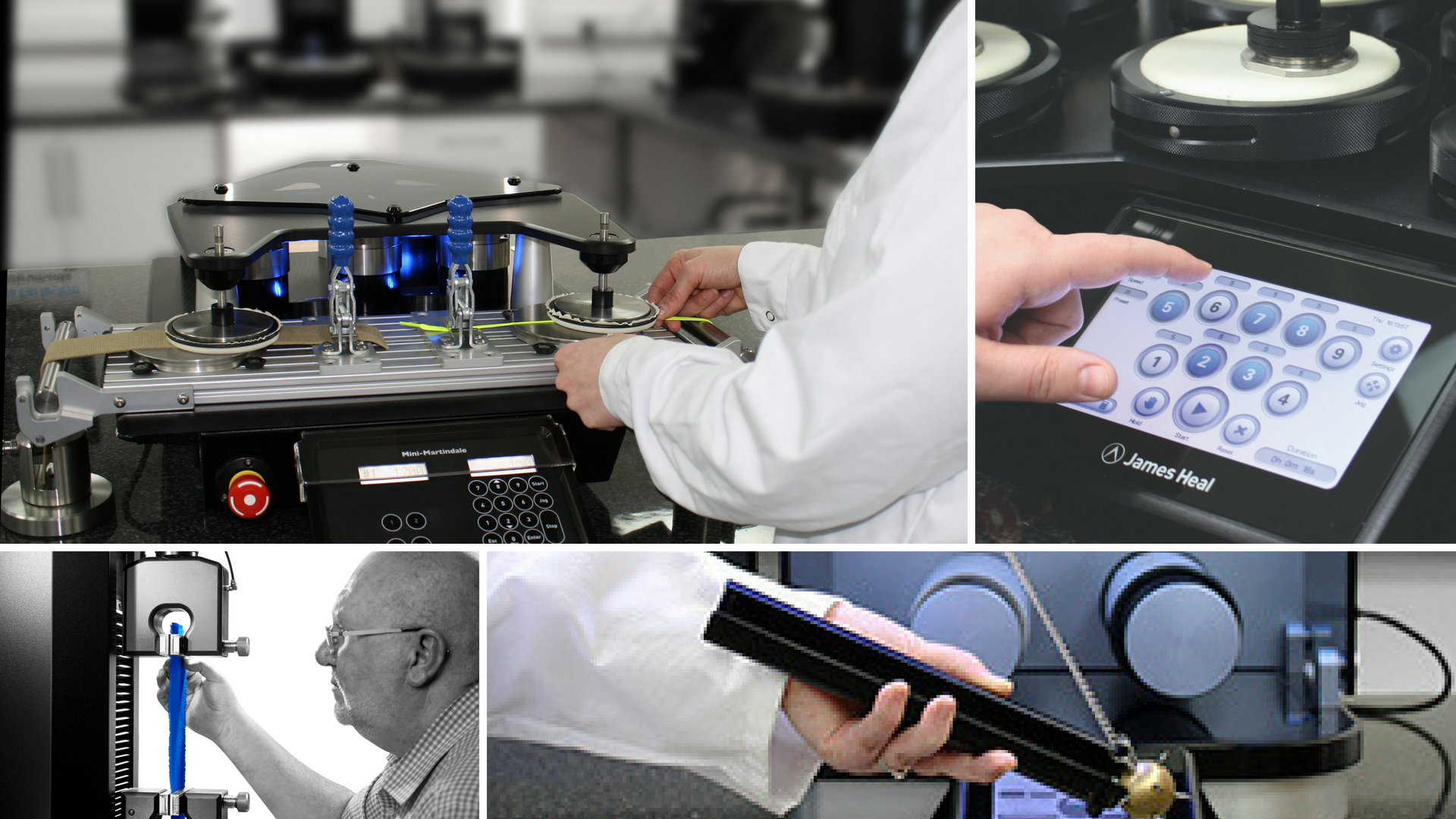
"If only the most basic Shrinkage and Colour fastness tests are to be done this may be possible in two rooms: a Wet Laboratory where the tests are done, and a Dark Room, where Fastness and Colour pass-fail/colour continuity assessments are carried out," says Peter. "In this situation, some technical requirements may be compromised. If this happens, there has to be an acceptance that some accuracy may be sacrificed."
"However, some people find it hard to accept the concept of having a separate Dark Room - but the cost of this is small when one considers the cost of rejects caused by inaccurate fastness grading or poor shade matching/roll to roll colour continuity,' adds Peter. 'All of these criteria can be strongly influenced by the environment in which they are carried out."
Many test methods such as Tensile Strength, Extension and Recovery, Abrasion and Pilling require that the test instruments are located in, and the test itself is carried out in, an environment of 65% RH and 20 Degrees C. This is often called a 'Conditioned Laboratory'.
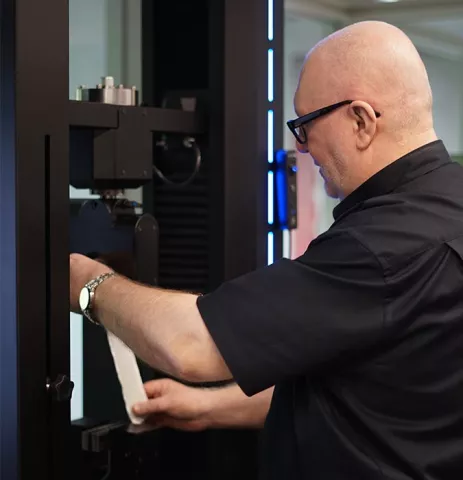
Conditioned laboratories
The next logical step, explains Peter, is a third room where the environment is closely controlled so that influences like high summer temperatures and high humidity in the 'rainy season' cannot adversely affect the test results.
"Many Test Methods such as Tensile Strength, Extension and Recovery, Abrasion and Pilling require that the test instruments are located in, and the test itself is carried out in, an environment of 65% RH and 20 Degrees C. This is often called a 'Conditioned Laboratory'."
However, as Peter elaborates, moisture in the atmosphere can significantly affect the results from these kinds of tests. "This is why all Independent Commercial Test Houses perform these kind of tests in controlled environments. The only way to minimise disputes with Buyers and reduce the amount of re-processes, rejects, discounts and claims is to follow as closely as possible the procedures and methods used by the Buyer and/or the Independent Laboratory he is using."
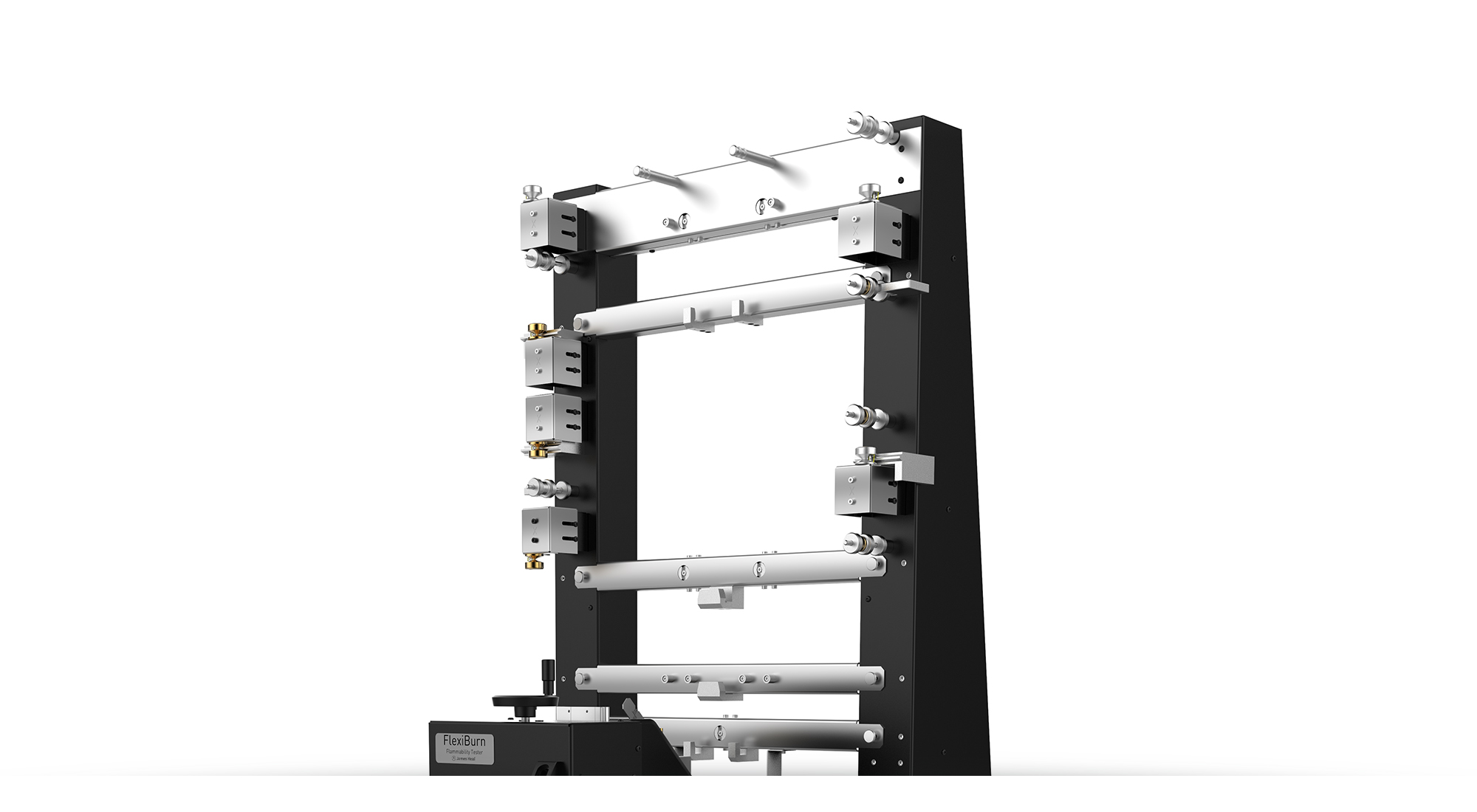
What aspects of technical control are best located in separate rooms?
"Spectrophotometers, Laboratory Dispensers, Lab Dyeing and Finishing Apparatus, Flammability Testers, Complex Analytical Procedures; Highly Accurate Weighing are all aspects of technical control that are best located in separate rooms," explains Peter.
Our network of contacts in the textile industry provides James Heal with massive resources, so we're ideally placed to provide comprehensive assistance and support to customers whether they are setting up a laboratory for the first time, or whether they are an established customer.
Final thoughts
At James Heal, our team of Technical Specialists have a combined experience of more than 120 years in testing and quality management in factories, commercial laboratories, retail brands and research and development.
Trusted by leading brands, retailers, manufacturers and laboratories in over 70 countries, since 1872 we've been on a mission to improve every aspect of materials testing, so our customers can achieve consistent and accurate results, every time.
Our worldwide chain of Channel Partners is similarly experienced in the same fields and our network of contacts with independent laboratories, buyers and specifiers, testing management committees and others in the textile industry provides James Heal with massive resources.
These ensure that we are ideally placed to provide comprehensive assistance and support to customers whether they are setting up a laboratory for the first time, or whether they are an established customer.