In our latest instalment of our Your Questions Answered series, we explore the subject of Light Fastness Testing.
During our recent Fundamentals of Light Fastness Testing Webinar, which was conducted by our Business Development Manager Alex Mitchell, we were asked a number of interesting and informative questions.
We have compiled the answers for you to read below. The key topics covered were:
- AATCC Fading Units - Timings
- Purified Water
- Measuring Photochromism
- Measuring Thermochromism
- Blue Wool Standards Timings
- Xenon Arc Lamp Lifespan
- Which methods use blue wools?
- Changing lamps and filters
- Patchy visual colour change
- ISO 105 B02 Method 2 vs 5
- Black Panel and Black Standard Thermometer
- Establishing exact times for testing
- AFU and correlation to elapsed hours
- Disparity between instruments
- Using a spectrophotometer
- The difference betweem ISO 105 B02 & AATCC 16.3
Q: As per AATCC 16.3-Option 3, we know 20 AFU (AATCC Fading Unit) Light fastness tests normally complete in 20 +-2 hrs, when visiting a factory I saw their AATCC 16.3 20 AFU light fastness complete after 28 hrs. Why would there be such a big difference?
A: The irradiance is probably less than 48wm2, 3456 kJ total radiation is required for 20 AFU. However 1 AFU is not necessarily an hour - this information is included in the standard and we would recommend referring to it for more information.
Q: What are the requirements for the purified water needed to run a xenon uv test?
A: For this test, you would need ISO 3696 Grade 3 water as a minimum. If mains water is used the mineral content in the untreated water will result in impurities being attached to the glass in the form of a white powder which will severely compromise the test results. It can also damage your testing instrument.
Q: How do you measure the light fastness for photochromic textiles?
A: Photochromism is defined as the light induced reversible change of colour, it is a temporary fading of fabric. Photochromism is taken into account in the standards by specifying that they should be allowed to cool & recover before grading. Each standard will set a duration of time for this.
Q: How did you measure the light fastness for thermochromic textiles?
A: Thermochromism is defined as a reversible change of colour when heated or cooled. Although not specified in the standards, the same should be followed as for photochromism allowing them to cool & recover before grading.
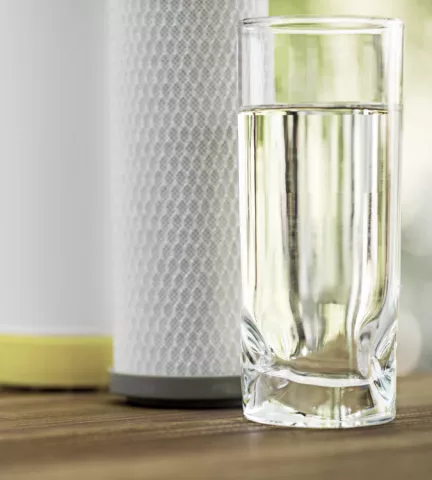
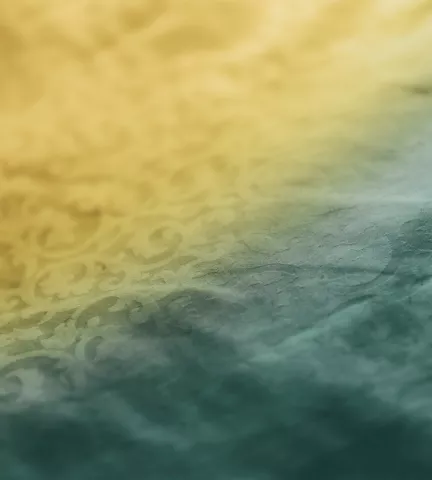
Q: How many hours would it approximately take for a Blue Wool Standard 4 to achieve a Grade 4 and a Grade 3 at 40% Relative Humidity.
A: For Blue Wool 4 using controlled irradiance of 42W/m2 40% RH and BST of 47DC as per ISO 105 B02 A1, Grade 4 would take approximately 40 hours, and Grade 3 would take approximately 80 hours.
Q: What is the lifespan of the xenon arc lamp?
A: We advised to check the lifespan of your xenon arc lamp before commencing testing, as although good light fastness testers will be set up to compensate for a lamp becoming less bright by adjusting the power to increase brightness, there ultimately comes a point where the irradiance can no longer be maintained. Lamps should last for approximately 1500 hours when run on ISO 105 B02 A1 42wm2.
Q: Which Test Methods refer to hours/time and which Methods refer to Blue Wool References?
A: Most textile standards are based on blue wools, whereas many automotive standards are based on dosage of radiation (time). Controlled irradiance is needed for this type of testing, so a radiometer like James Heal's SolarSens is required. ISO 105 B02 - Method 5 refers to irradiance dosage.
Q: At what frequency should users be changing Xenon Lamps, KG1 Filters, Borosilicate Cylinder and Air Filters?
A:
- Lamps: change at approximately 1500 hours of testing when run at ISO 105 B02 A1
- KG1 Filters: change at 3500 hours of testing
- Borosilicate Cylinder: This has no lifespan so doesn't require changing, just keep it clean and undamaged
- Air filters are environment dependent
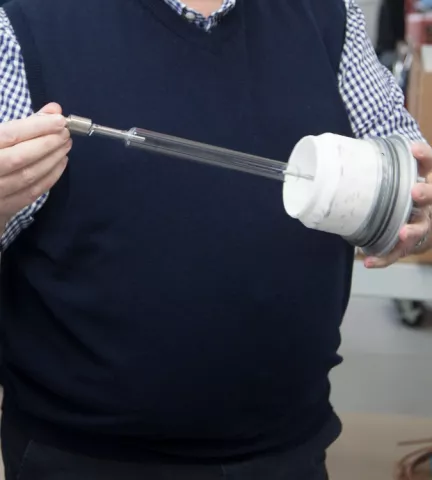
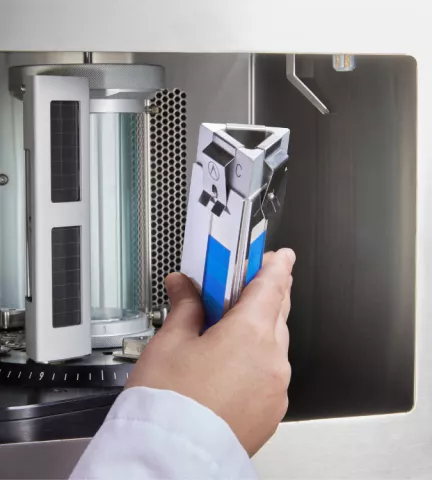
Q: What could cause a patchy visual colour change, but not all over and normally around pockets or zip area. This was on 100% cotton shorts and the navy colourway had pink patches in these areas after a few wash and wears - testing ultimately stated that the fabric was ok?
A: This sounds like the fabric is contaminated in someway or there is a reaction with any metallic elements on a zip or pocket rivet. If it's navy blue and it is going pink, it does lean towards the dye being destroyed in someway - this is assuming that it has faded to pink and it is not a pink stain.
Q: Can you explain the main difference between ISO 105 B02 Method 2 and Method 5?
A: Method 2 uses blue wools, it is described in the standard as, 'This method is used when a large number of specimens have to be tested simultaneously. It allows a number of specimens differing in colour fastness to be tested against a single set of blue wool references, thus conserving supplies.' Method 5 is based on dosage of radiation (time), the standard states, 'This method is suitable to check conformity to agreed-upon radiant energy levels.'
Q: What is the difference between Black Panel Thermometer and Black Standard Thermometer?
A: The temperature indicated by the black-panel or black-standard thermometer depends on the irradiance produced by the apparatus light source and the temperature and speed of the air moving in the test chamber.
Black-standard thermometer (as favoured by ISO) temperatures generally correspond to those for the exposed surface of dark samples with poor thermal conductivity.
Black-panel thermometer (as favoured by AATCC) temperatures generally correspond to those for dark coatings on metal panels. AATCC 16.3 Option 3 Uses this and light fastness customers specify this most frequently at conditions used in typical exposure tests, the temperature indicated by a black-standard thermometer will be higher than that indicated by a black-panel thermometer.
Because black-standard thermometers are insulated, their response time for temperature changes is slightly slower than for a black-panel thermometer. You can see the physical differences on the graphic below:
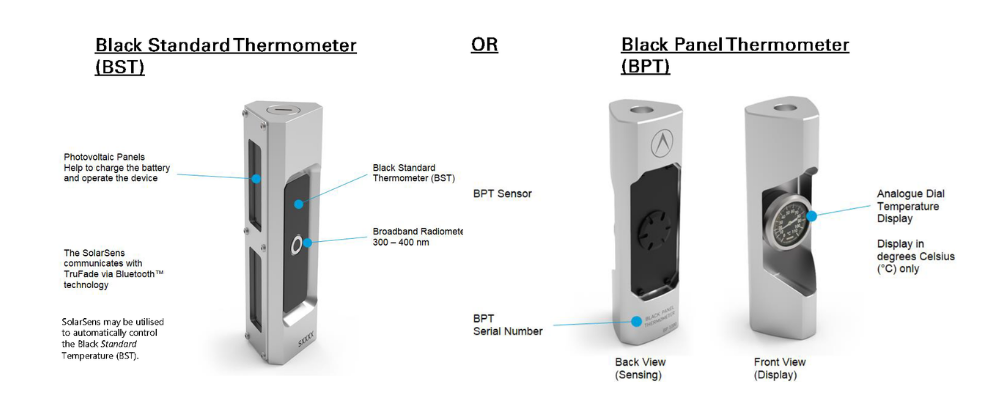
Q: I want to know the time of testing for my textile, and sometimes I have a problem with the exact time needed for the test? How can I realize that?
A: In this situation we would recommend using controlled irradiance, as the output from the lamp is the same all the time. If you use blue wool mode/nominal power mode, as the lamp ages and if the power isn't compensated, the time to fade will take longer.
Q: In combination to the AATCC standard I've heard about the unit AFU. Can you explain it and is there a correlation to the elapsed hours?
A: AATCC defines an AFU as 'a specific amount of exposure made under the conditions specified in various test methods where one AFU is one-twentieth (1/20) of the light-on exposure required to produce a color change equal to Step 4 on the Grey Scale for Color Change'. To fully understand how AFUs work, along with Fading Unit and Light Exposure Equivalents, we recommend reading AATCC 16.3-2012, specifically Page 45 3.2, Page 46 5.1 Table 1 and Section 41. Unfortunately we are not allowed to replicate the standard here.
Q: Quite a lot of clients ask about the duration of exposure e.g. grade 4 & 5, but we find it's not the same for all testers. How do you explain this to the client?
A: If all machines are using the same conditions correctly then they should all fade at the same time. If you use controlled irradiance, as the output from the lamp is the same all the time, then times to fade will be more consistent. If you use Blue Wool mode/nominal power mode, as the lamp ages and if the power isn't compensated, the time to fade will take longer. This is why blue wools are used in textile methods - because we are taking the fading to a reference point rather than to a defined time.
Q: Is it common to use spectrophotometer for light fastness? Can you give any information how to use spectrophotometer for assessment?
A: For more information on this, refer to standard ISO 105 A05 for colour change. For use of a spectrophotometer contact individual suppliers such as Exrite (e.g. model Ci7860) or Datacolour.
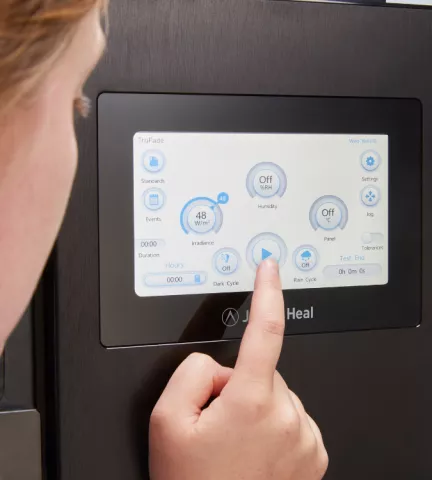
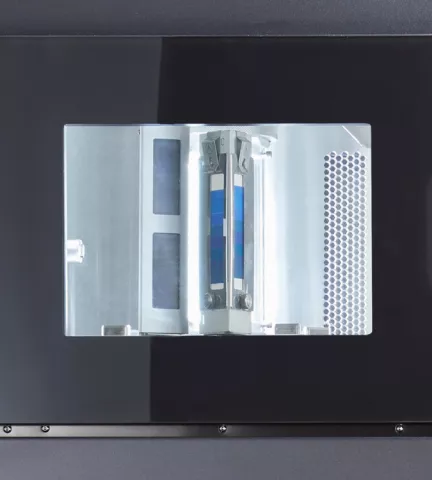
Q: What is the difference between ISO 105 B02 and AATCC 16 Option 3?
A: The ISO 105 B02 has five test methods, AATCC 16 has six test options, in which the option 6 in AATCC 16 is approximately similar to ISO 105 B01 and option 2 is equivalent to ISO 105 B02. AATCC Exposure to radiant energy = B02 Method 5; Exposure using a reference specimen = B02 Method 4 and Exposure to light classification is Method 1 (3 & 4).
Both tests carry out essentially the same test just with slightly different methods, however, these methods differ too greatly for the results to be directly compared. Comparisons should only be made between results from the same standards body, same specific standard, same part and same option.
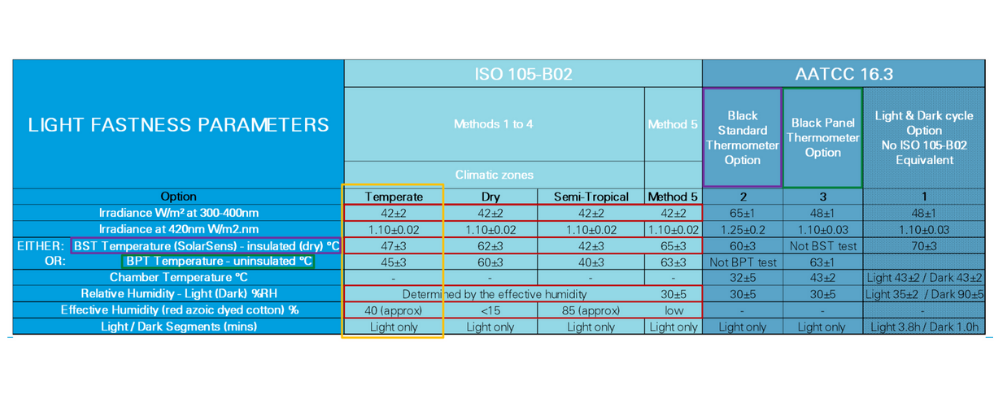
We hope these questions and answers around Light Fastness Testing have been helpful.
If you missed this webinar, you can watch it on demand at a time that suits you - click here to access the on-demand webinar.
If you want to find out more about the TruFade, please contact us here.