Textile manufacturers, their suppliers and customers all have an essential need for effective flammability testing - for quality control, research and development and certification purposes.
In this technical article, as part of our TechTalk series, our Technical Specialist, Peter Goodwin, explains the risks and hazards associated with this type of testing, the combustion process, incentives to comply with flammability regulations and specifications.
We also explore recent changes to flammability standards, along with the relevant legislation.
The importance of testing
"Homes and workplaces are filled with materials that can and will burn if ignited", explains Peter.
For example, upholstered furniture, clothing, drapery fabrics and toys, are involved in numerous fire injuries each year; yet most of these accidents could be prevented. Most textile fibres used in clothing can burn, some more easily than others.
A significant number of clothing fires occur in the over 60 age group predominantly involving nightwear. Approximately three quarters of clothing fire-related deaths occur in the 65-and-older age-group, with females being 55% more likely to be involved in clothing fire accidents.
But why? One explanation could be that females in this age group are more likely to wear loose-fitting, flowing garments, which can easily catch fire near the smallest of open flames, such as matches, cigarette lighters and candles - which also happen to be the major sources of clothing ignition, following by gas cookers, open fires and space heaters.
"The garments most commonly associated with clothing ignition fatalities are items of nightwear," explains Peter.
Approximately 10% of clothing flammability accidents are estimated to be fatal - and occur almost entirely in the 65+ age group
In addition, some fibre blends should be avoided when contact with fire is likely, says Peter.
For example, polyester/cotton blends can produce an injury far greater than if either of the individual fibres were used alone. "Put simply, the cotton content burns easily, with the carbon char forming a 'scaffold'. The polyester fibre, which would normally melt and shrink or drip away, continues to add fuel to combustion process, spreading fire or increasing injury," Peter explains.
Interestingly, the type of fibre involved in burning accidents is divided equal between natural and synthetic fibres (42% each). Cotton is involved in 29% of cases, polyamide in 26%, polyester/cotton blends in 13% and wool 6%, with unknown compositions making up the balance. However, these comments are for guidance only, emphasizes Peter; and "should not be taken as an authoritative interpretation of the standards or the legislation".
Flammable textiles are safe provided they are not exposed to flame or extreme heat. Likewise, fire is safe provided we are not directly exposed to the flame, heat or toxic fumes and smoke. It is the proximity between the textile and heat source that is the concern.
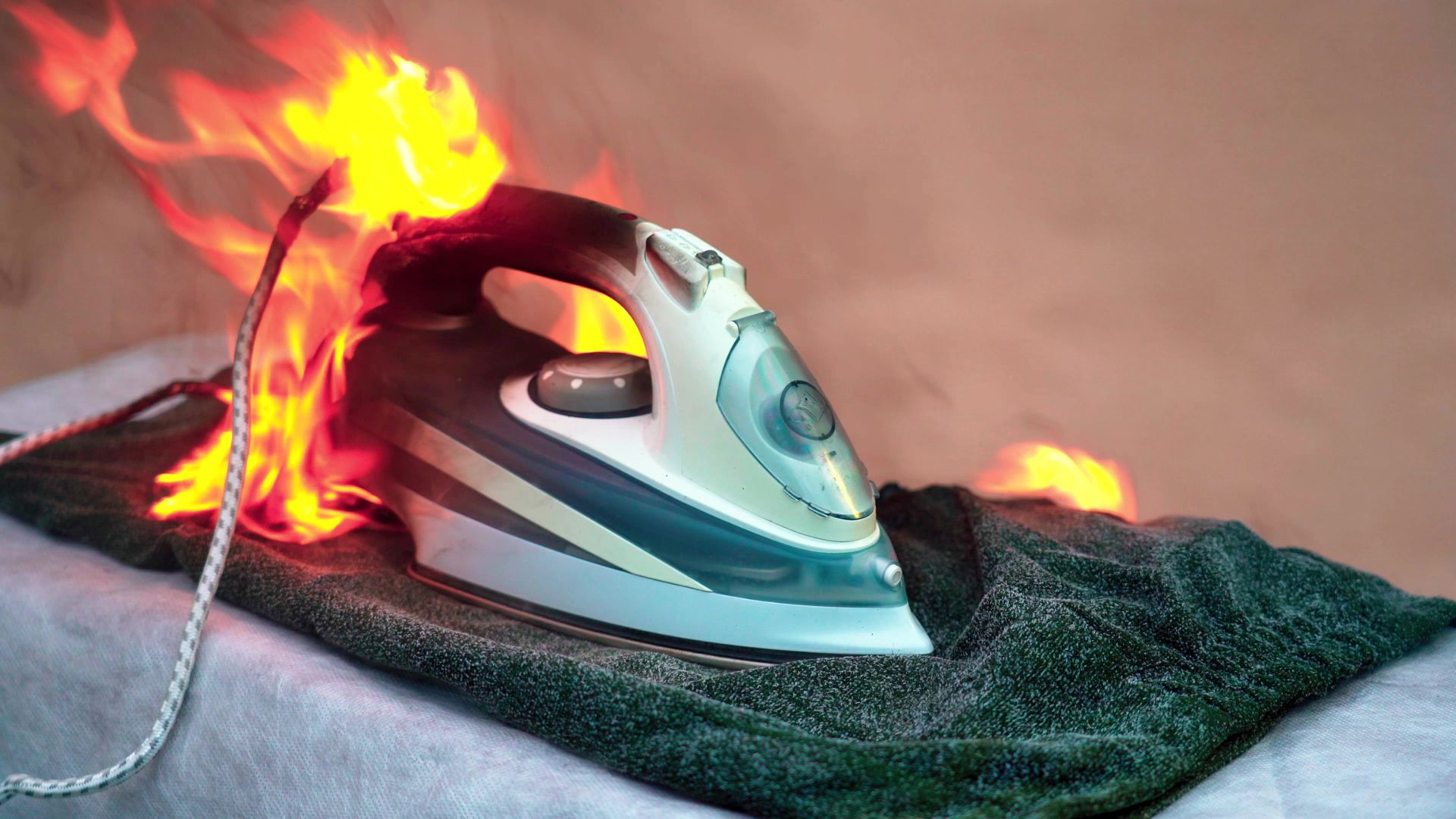
Risk and hazard
When consumers look at clothing, they are generally unaware of any risk from the clothing should they be exposed to fire. They are also unlikely to have any expectations regarding its flammability.
There is, therefore, a latent risk involved if a fabric is highly flammable.
Flammability is a factor that affects the probability (risk) of becoming exposed to the fire hazard. Flammable textiles are safe provided they are not exposed to flame or extreme heat.
Likewise, fire is safe provided we are not directly exposed to the flame, heat or toxic fumes and smoke. It is the proximity between the textile and heat source that is the concern.
What is combustion?
One generally accepted definition of combustion or fire is "a process involving 'rapid' oxidation at elevated temperatures, accompanied by the evolution of heated gaseous products of combustion (smoke and fumes), and the emission of invisible and visible radiation (heat and light)."
The reaction needs fuel, heat and oxygen to create fire. If any one of them is missing, there can be no fire. The combustion process occurs in two modes, flaming and non-flaming (smouldering or glowing embers).
Either one of these can lead to the other mode given the appropriate conditions. Flame-retardant chemicals are designed to interfere with combustion process by influencing the Fire Triangle in one or more ways.
Compliance should never be assumed: hard evidence in the form of test reports from accredited test laboratories should be insisted upon.
Regulatory compliance
Recognising that regulatory compliance is not a passing fad, savvy textile manufacturers have focused their efforts on building systems that can manage and adapt to new and changing regulations and requirements. By proactively incorporating compliance requirements early in the design process, these companies have positioned themselves for success in line with regulations and specifications.
Failure to address compliance with a strategic, long-term solution will simply defer the cost until some future time, creating competitive risk, tighter timeframes and higher costs.
A consequence of delay will be that substantially less time will be available to comply with the next set of regulations, further increasing the risks and costs.
Compliance can never be assumed: hard evidence in the form of test reports from accredited test laboratories should be insisted upon.
Testing costs may appear high or pointless but a few tests are a small price to pay when the costs of non-compliance can be disproportionately high. Companies could be faced with court expenses, fines, loss of stock, product recalls, loss of customer confidence and future orders.
Responsibility for compliance begins with the first supplier in the chain. By not exercising due diligence, a company may be putting consumers at risk of injury. It is essential that companies know exactly which national or international standards their products must meet in order to achieve compliance and start testing.
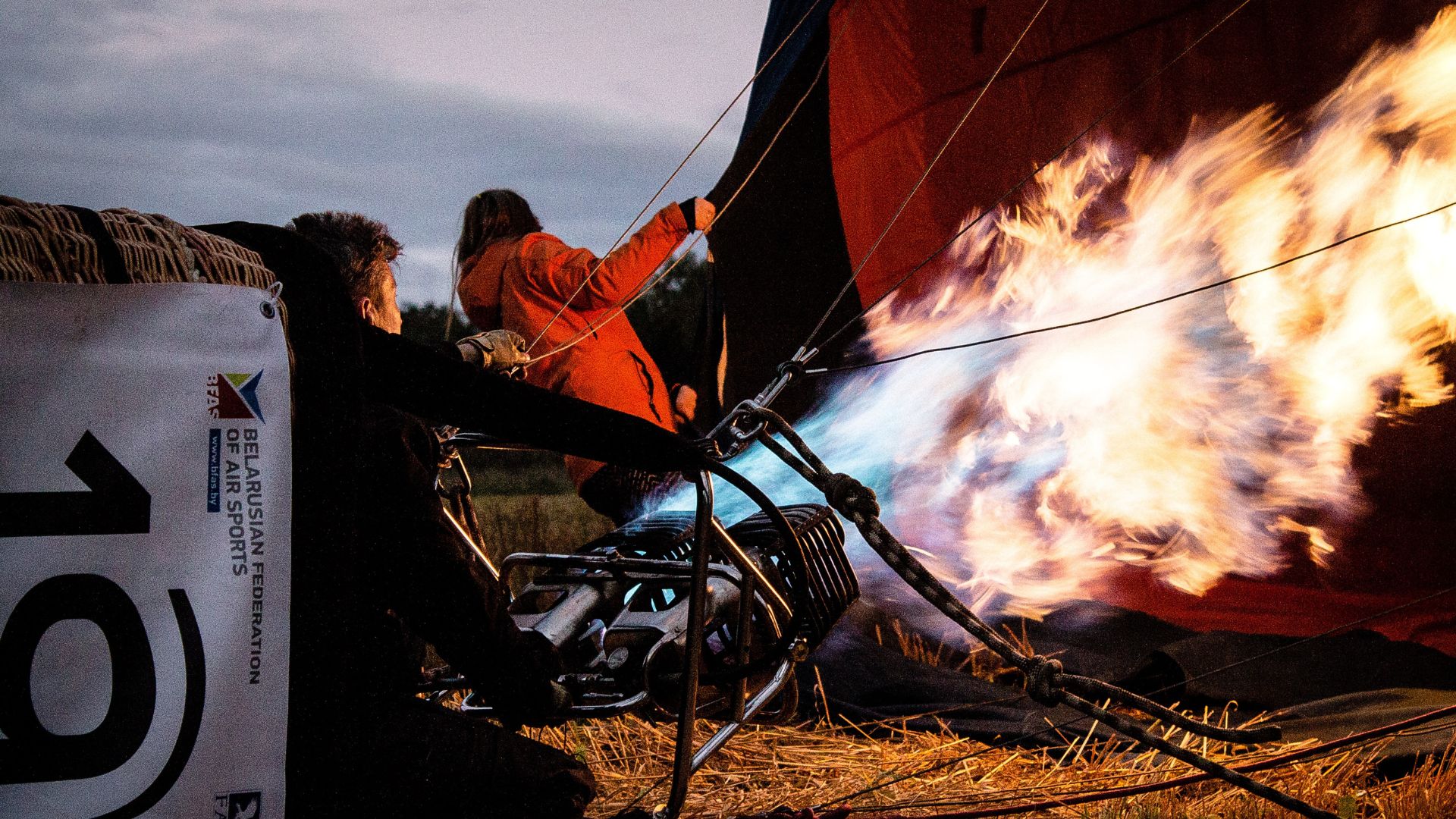
Any fabrics composed of cellulosic fibres, such as cotton and viscose, must be treated with a flame-retardant agent if it is to be used in production of children's nightwear.
Factors influencing the flammability of textiles
Textile flammability is not a simple function from which the burning behaviour of the textile can be predicted under all circumstances. The subject is complex and has resulted in the development of a wide spectrum of test methods, some of which are specific to particular end-uses.
The processes applied to textiles to produce the final product give an indication of the factors which affect textile flammability: fibre or fibre blend, the fabric construction, the fabric weight, napped or pile surface, other surface finishes, the article design, any other materials used in the composite, how the article is cleaned. Any of these factors can affect the flammability in either an adverse or a favourable manner.
One method of ranking the flammability of textile fibres is by 'Limiting Oxygen Index' (LOI).
Air contains about 21% oxygen, so any fibre having a LOI below 21% will burn more readily than those with an LOI greater than 21%. For example, cotton has an LOI of 20%, wool 26%, Proban-treated cotton 28-30%, Zirpro-treated wool 32%, and aramid (aromatic polyamides) 28-34%.
The method described in EN ISO 4589-2 gives more details of LOI.
The use of flame-retardant treatments and inherently flame-retardant fibres to produce textiles with reduced flammability is important when the textile is to be used in an area with higher than normal risk of ignition. For example, polyester fibre can be modified with flame-retardants during its formation, to produce fibres which produce no molten drips, thereby reducing the spread of fire.
A typical example of this would be curtains made from flame-retardant polyester. Technical textile fibres such as Nomex (poly meta-phenylene isophthalamide) are used in applications such as fire-fighting, fire protection and defence.
Review of flammability testing of textiles
The flammability of textiles is one of their most critical issues. Poor performance or the incorrect choice of clothing can lead to serious injuries or even death in fires.
The continuing growth in health and safety legislation can be seen as an attempt to restrict the number injuries and deaths. Accompanying the legislation is a large array of standard test methods and performance standards (specifications).
The following is only a brief summary of those available but shows the extent and coverage of the standards, with the aim of informing and protecting the textile user. An increasing number of these standards have become harmonised as European Standards (EN). When a standard is adopted as an EN, any conflicting national standards must be withdrawn.
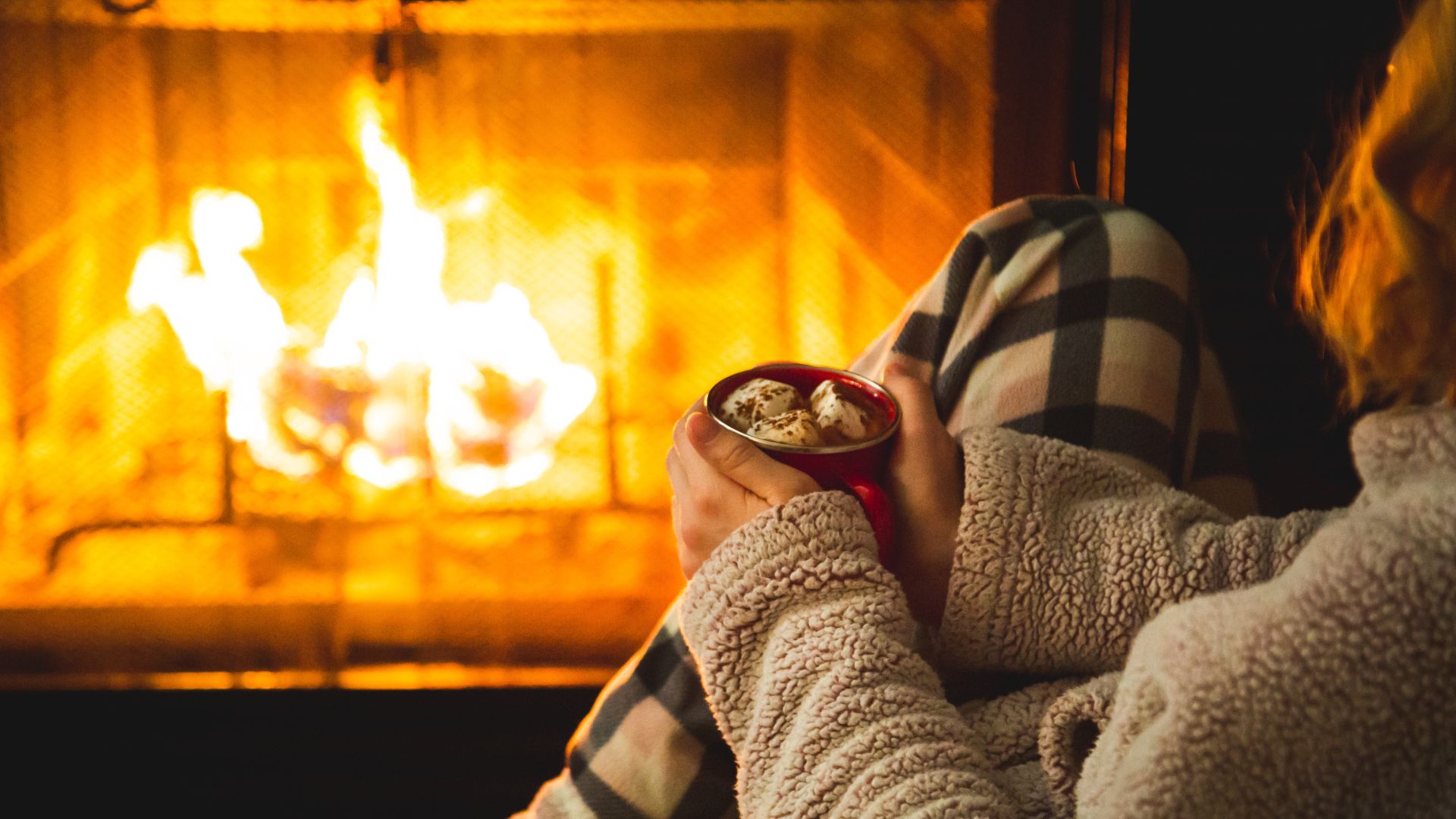
The Nightwear (Safety) Regulations and EN 14878
In the UK, nightwear is covered by The Nightwear (Safety) Regulations 1985 (as amended) which in turn refers to BS 5277:1984 (and BS 5438:1976).
The EU has harmonised the flammability requirements of nightwear with a document known as 'EN 14878:2007 Textiles - Burning Behaviour of Children's Nightwear - Specification'. It considers those items of nightwear and nightwear fabrics that could pose a significant risk of injury to children and adults from the hazards presented by the potential to ignite. As nightwear is normally worn directly on the skin, there is an increased risk of burning injuries in cases of ignition.
Loose and napped garments such as nightdresses, nightshirts and dressing gowns provide a large surface area for ignition and the risk of ignition is higher than for daywear textiles. Any fabrics composed of cellulosic fibres, such as cotton and viscose, must be treated with a flame-retardant agent if it is to be used in production of children's nightwear.
Before testing, any such fabric is washed 12 times, to determine the durability of the treatment. If the nightwear is composed of synthetic fibres then it is washed only once. After washing and drying, fabric specimens of 670mm x 170mm are prepared -- three from the length direction and three from the width direction. If a sufficient length of fabric is not possible, the specimen can be prepared from up to three pieces joined together with staples. The specimens are then conditioned for 24 hours.
The flammability testing apparatus must be situated in a draught-free environment. After fixing the specimen to the pin frame, and setting up the cotton marker trip threads, a butane flame of 45mm height is applied for 10 seconds. In many cases, the performance is evaluated according to the rate of flame spread. In order to comply with the Nightwear (Safety) Regulations, according to BS 5722 the time taken to reach the second (300mm) marker thread should be 25 seconds or more and the time taken to reach the third (600mm) marker thread should be 50 seconds or more.
The regulations refer to standards over 20 years old: BS 5722: 1984; BS 5651: 1978; and BS 5438: 1976 (as amended April 1981), but still offer a sound standards framework for the regulations.
It should be noted that fabrics of different fibre compositions are likely to react to the test in different ways.
Treated cellulosic fabrics will char but not ignite or melt. Fabrics composed of polyamide (nylon) or polyester may melt away from the flame.
Nightwear which may or may not meet the flammability performance requirements should have a label saying 'keep away from fire'. Nightwear which meets the flammability performance requirements has a label quoting 'low flammability to BS 5722'. Note that a label that reads 'low flammability' does not indicate a completely flameproof product and all clothing should be kept away from fire.
Children's nightdresses and dressing gowns, which must meet the flammability performance requirements, do not need to carry a label.
In addition, any nightwear which has been treated with flame-retardant, must bear a label with the words 'Do not wash at more than 50 degrees C. Check suitability of washing agent'. This may seem like a trivial statement when so much care has already been taken to provide a safe garment. However, soaps can leave an insoluble fatty film on the fibre/fabric surface which can be flammable. This may also apply to some fabric softeneners and conditioners. In addition chlorine bleaches are to be avoided as these can be retained by the flame-retardant chemical and impair its performance.
The regulations in the UK are enforced by the Trading Standards Officers (TSOs).
Failure to comply can result in fines of up to £5,000 (approximately $7,250) and/or a six-month custodial sentence.
EN ISO 15025 Protective Clothing
In relation to occupational and personal safety, a useful example is 'EN ISO 15025 Protective clothing - Protection against flame - Method of test for limited flame spread', which superseded the EN 532: 1994.
The test method, as with many others, is based on ISO 6940. The method employs both surface and edge ignition tests.
The specimen, with dimensions of 200mm x 160mm (or 80mm), is supported on a mounting frame with four pins. Cellulose filter paper is employed in the assessment of flaming debris. A propane flame of 40mm vertical height is applied for 10 seconds. Observations -- such as afterflame and afterglow times, if any flaming reaches the upper or vertical edges of the specimen, if holes are formed (surface ignition only), and if there is any flaming debris -- are made during and after flame application.
The method is used to determine whether or not any flame spreads to the edges of the specimen (limited flame spread).
The rate of flame spread is not determined. A method for measurement of char length is given in the annexes to the standard.
EN 1103 Apparel
The standard 'EN 1103: 2005 Textiles - Fabrics for apparel - detailed procedure to determine the burning behaviour' is a test method which refers to 'ISO 6941 - measurement of flame spread properties of vertically oriented specimens'.
EN 1103 modifies ISO 6941 to be only a surface test, in which the flame from commercial propane gas is applied for 10 seconds. Any flaming debris is also assessed with the aid of cellulose filter paper beneath the specimen. The recent revision of EN 1103 now includes testing flammability before and after cleaning (as and when recommended by the care label).
However, this is not intended as an assessment of the flame-retardant durability. In many cases the amount of testing required will double and more fabric will be required for testing.
Another major change is to the conditioning of specimens. The standard now requires a minimum of 24 hours at 23 ± 2deg C and 50 ± 5% RH. Previously the 20/65 standard was employed.
There are still some remaining contentious issues regarding the handling of specimens - particularly knitted fabrics, the positioning of specimens on the pin frame and the number of pins on the supporting frame.
Final thoughts
Clothing might be exposed to fire because of the failure to supervise or to educate.
However, the very purpose of warnings and safety information is to educate consumers so that they can make informed decisions, such as opting not to purchase the garment, or only to wear the garment when they will not be exposed to open flames, or to know what to do if the garment catches on fire.
Lack of labels equates to lack of information upon which to make those informed decisions if given a choice.
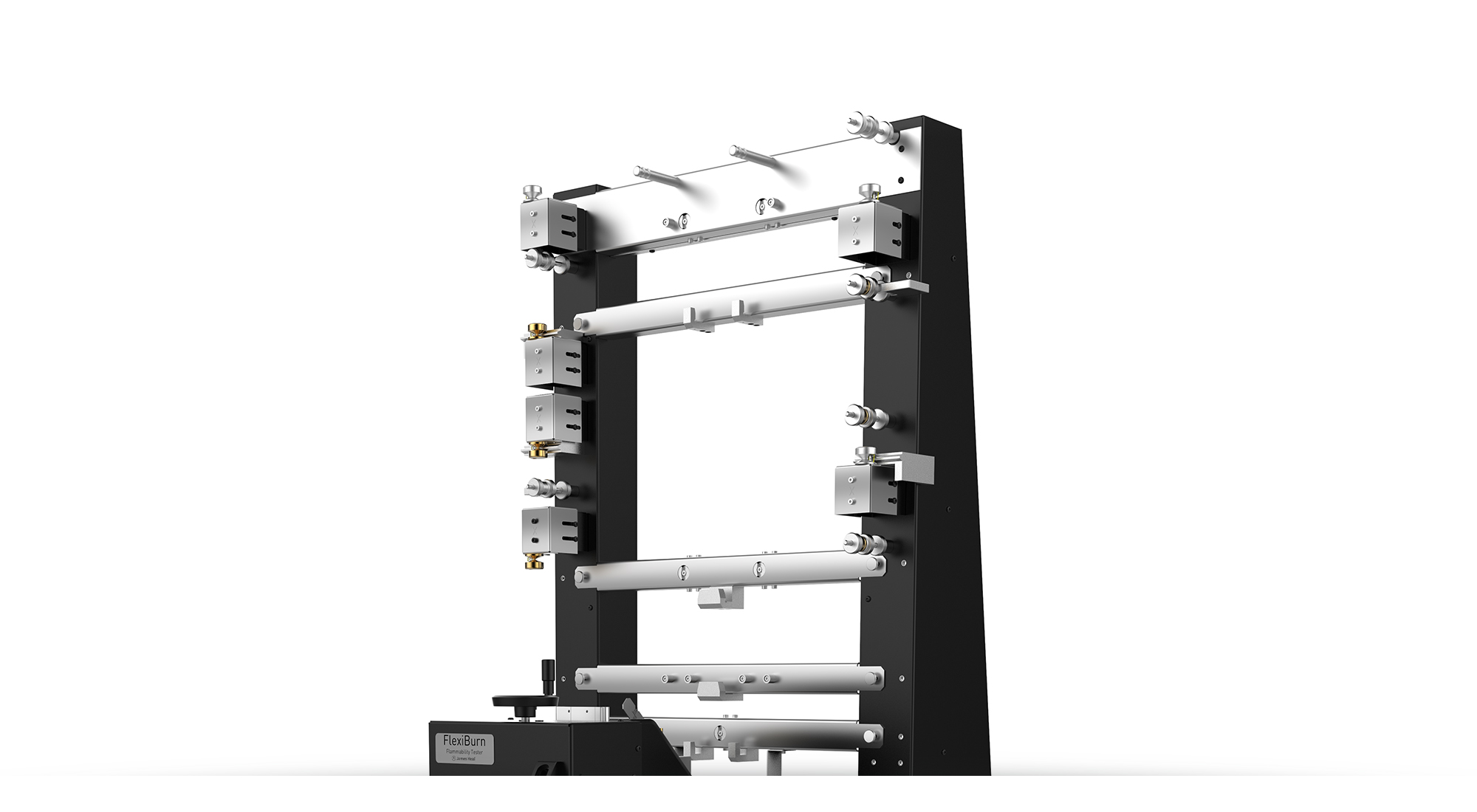
Discover FlexiBurn
Test equipment such as FlexiBurn can help retailers and clothing manufacturers meet the needs of the above standards.
Accessories can ensure that testing is carried out in accordance with national and international standards.
Contact us today
Get support from the textiles testing experts and talk to us about your testing requirements.