In the textiles industry, external circumstances are ever-changing. These can involve changes to standards, legislation changes, new innovation and technology, issues with the environment and politics - to name some. It's therefore vital for testing laboratories to survive and keep up with the competition. You need to respond to such changes by developing your laboratory staff into knowledgeable, well-trained laboratory technicians.
Training to keep staff updated on the skills needed to meet business demands, address changing industry trends, and use new technologies is a crucial component of any textile testing laboratory - whether an independent lab or in-house lab within the factory. 'Lab managers can get the most out of training programs by being proactive in identifying relevant training needs, leveraging networks of training experts, and fostering a culture of continuous learning', says Peter Goodwin, Technical Specialist at James Heal.
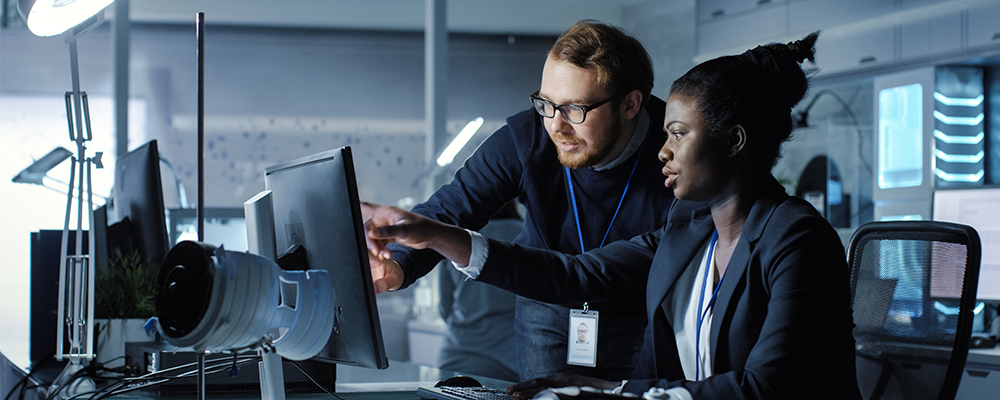
Why People Matter
'However well designed a Laboratory is, and however good the instruments are; the results that it produces will finally depend on how good the people are that work in it', says Sara Williams, Technical Specialist. 'This does not always mean that the Laboratory staff should be University Graduates; but in order to provide accurate and efficient analysis, laboratory technicians need to keep up to date with trends and innovations, should have a solid understanding of textile fundamentals, laboratory equipment and procedures as well as a basic grounding of the same fundamental safety and operational training taken by colleagues in other parts of your organisation'.
Sara emphasises that it is more important, that they have a 'good standard of general education, that they have an 'eye for detail' and that they are able to follow procedures exactly, day in and day out. These are essential to ensuring the safety and quality of processes and products.'
Generally, lab technicians need the following skills according to Prospects.co.uk:
- Ability to work independently without supervision and with initiative
- Good observation skills and attention to detail
- A thorough and methodical approach to work
- The ability to record test results accurately and write reports of findings
- Teamwork skills
- The ability to use a wide variety of laboratory equipment
- Computer and word-processing skills
- An enquiring mind, with a willingness to learn and develop new skills
But how do you train and develop these skills in your laboratory team?
Communication is key in the laboratory setting
Peter adds that communication is the biggest part of training, and running an effective testing lab. 'Most test methods and communications from Export Buyers will be in English Language, so the Lab Chief should have good English and be able to communicate the needs of the documents that he receives into local language so that his staff can easily understand what is required.'
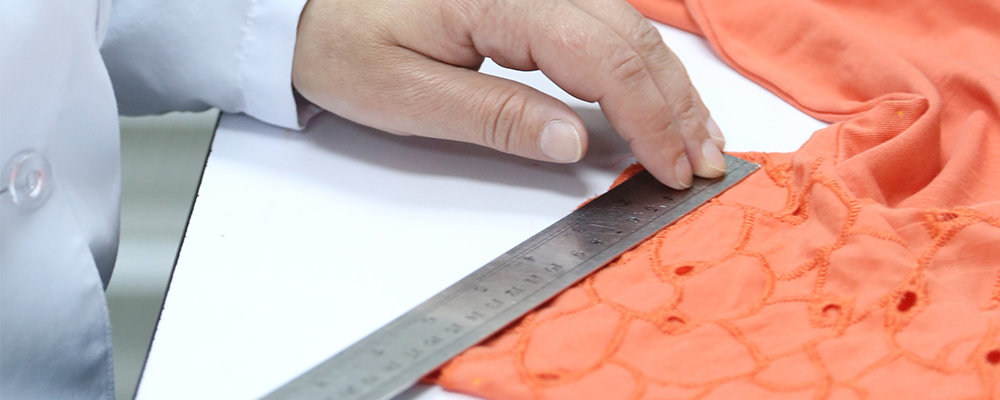
Who is responsible for delivering training?
'Whilst the supplier of the laboratory instruments and accessories will often train the technicians to operate the instruments the company has provided, they will not automatically train them to perform specific test methods', says Sara. 'The Lab Chief should take part in this training at the same time as the lab technicians. This training is best carried out during the installation of the instruments,'
Sara explains. Sara also emphasises that the supplier will not necessarily give explanations of what the results mean and what actions the technician should take when he/she has produced the results.
"This detailed applications training is very personal to the customer and to Buyers, and is therefore the responsibility of the customer to ensure that the Lab Chief has all of the information necessary to understand what is required of them and their staff. This should form the basis of internal training."
Maintaining accurate training records
'The Lab Chief should start and maintain a file for each employee that works in the Laboratory. This should be done in partnership with the individual concerned and should be used to monitor the individual's training progress', says Peter.
It should list all of the tasks that the individual is required to perform and should allow the Lab Chief and the individual the chance to assess how quickly the individual builds up experience and competence in these tasks. It should also highlight not just what the individual needs to do to progress, but also what the company needs to do to help the individual reach his target.
'Normally these things are assessed against a timetable which must reflect the needs of the company, yet must give the new recruit sufficient time to become competent and confident to do their job.'
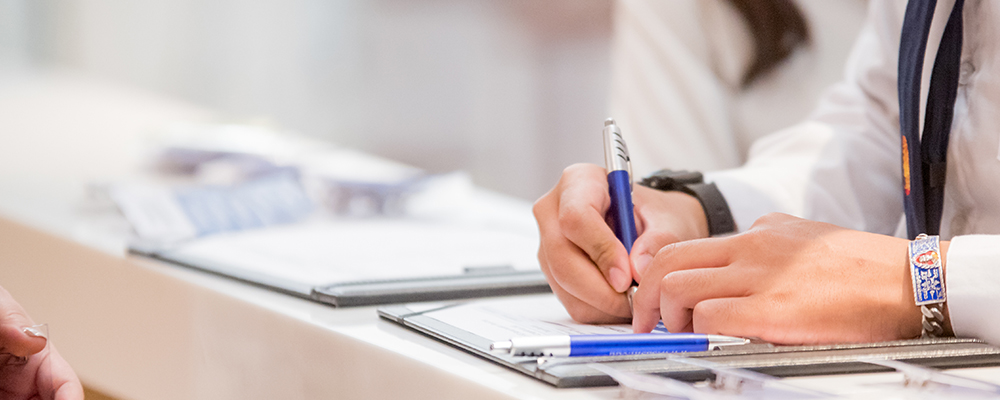
The Training Schedule
The Training schedule has to cover not only every detail of each Method and Procedure but must also ensure that the person understands the need to check/verify/ calibrate the apparatus, the way the Job/Procedure works and the background as to the important aspects of the Job/Procedure.
Peter GoodwinTraining and understanding in the Laboratory is vital in order to ensure that the work is accurate and that the results that can be relied upon. If the Lab is to be Accredited then it is often necessary or advisable to show these training and assessment records to the Accreditor.'
How often is training and assessment required?
The assessments of progress should be carried out on a disciplined and regular basis, certainly every week for a new employee and thereafter every two weeks extending to every month once the technician has demonstrated that he/she is progressing at the appropriate pace.
'In addition to the training and auditing of new recruits, it is equally important to ensure that even experienced technicians are performing correctly as time goes on. This can only be done by auditing the performance of all of the laboratory staff every six months to ensure that they are following the correct procedures and methods,' Sara comments.
Sara explains that this auditing is best done by a correlation exercise in which each individual carries out the same tests on the same products and produces complete and test reports showing gradings and numerical results. 'When each technician has completed his or her set of correlation tests the individual reports can be compared by the Lab Chief to ensure that the results from the different technicians are comparable, within the limits of normal experimental error'.
All of the above training and auditing information should be recorded on standard documents such as a Staff Training Record and a staff Appraisal Record. These should be logically filed for later reference between the Lab Chief and Technician and in a manner that also allows them to be shown to an Accreditor or external Assessor.
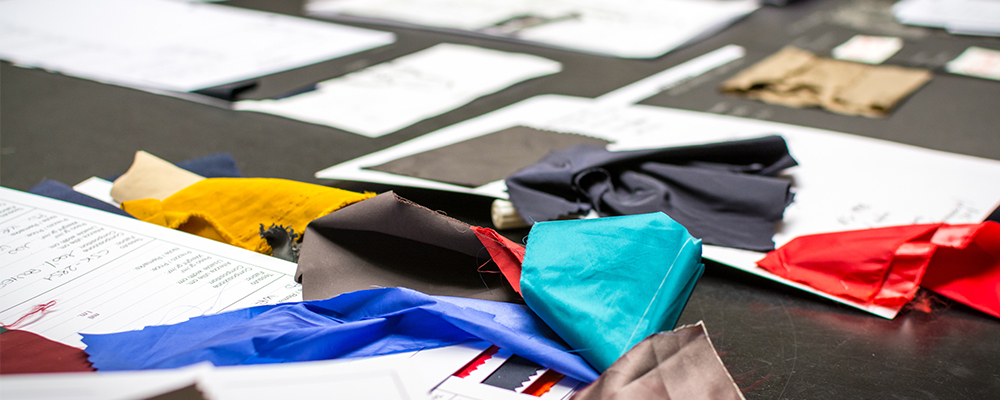
How to identify training needs
Training is required to prepare staff to respond to changes such as meeting new regulatory requirements and stay competitive in a technologically advancing market. Thus, lab managers should research industry trends to forecast future training needs. For example, Peter and Sarah regularly attend trade shows and talk to customers to stay updated with emerging technology and innovations in the industry. 'Technical staff members tend to be curious by nature and self-motivated learners. You should permit flexibility to allow your lab technicians to attend seminars, conferences, and technical meetings related to their areas of expertise.'
Another focus area for training needs is to fill skill gaps '
The lab chief should continuously assess workforce capability in terms of which skills are available, which new skills are needed, and which skills are at risk of being lost. From there, the lab chief can determine what the skills gaps are the type of training needed to fill that gap', says Peter.
Final Thoughts
The main benefit of training your laboratory team and conducting regular skills gap assessments is to improve safety within the lab, and to enhance productivity - to meet your customers' expectations and send a strong message to your customers about your organisation's commitment to meeting their needs.
We've discussed training in this article, and you may also enjoy reading our '12 step checklist to constructing a conditioned textile testing laboratory'. You can download this guide for free, here.
About the Authors
Sara Williams, Technical Specialist
As our 'Core Instrument Technical Specialist', Sara uses her experience within the garment & textile industry to provide expertise and support to James Heal's customers, colleagues and channel partners.